It’s time to start thinking about the future – and the future is now when it comes to artificial intelligence (AI) in manufacturing.
We’ve seen huge advances in recent years, and I’m here to tell you that the possibilities for the future are almost limitless.
AI is allowing manufacturers to increase automation, optimize production, and create more efficient factories.
And that’s just the beginning.
In fact, a recent report by Market and Markets predicts the AI in manufacturing market size to reach $USD 16.3 billion by 2027.
In this article, I’ll dig into the main aspects of AI in manufacturing.
We’ll take a close look at what AI is already doing in the industry and how it could be improved in the future. We’ll explore how manufacturing processes can be adapted to fit AI technology and what companies are doing to capitalize on it.
Finally, I’ll discuss the potential implications this technology could have on society.
So, get ready to jump into the exciting world of AI!
1. Automated Quality Assurance
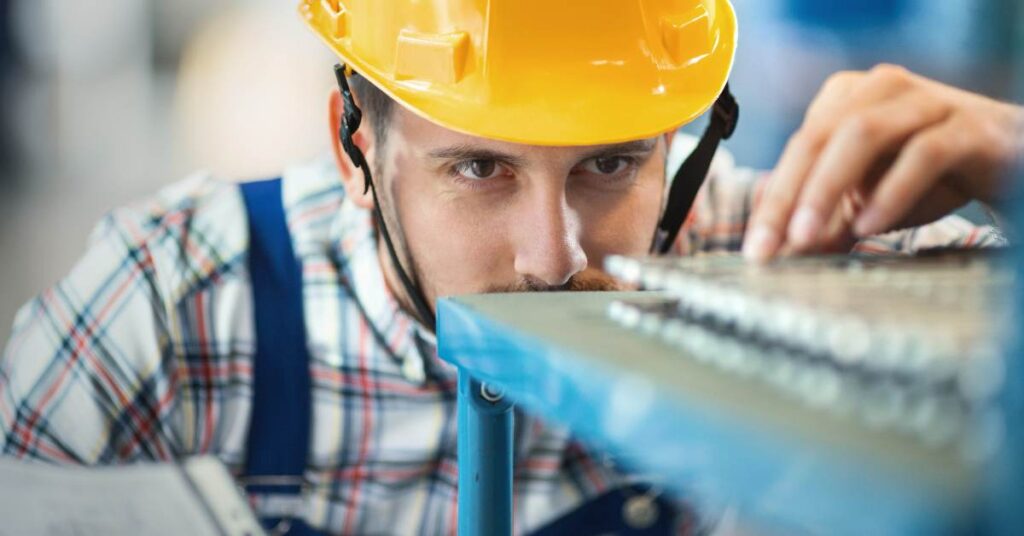
When it comes to the future of artificial intelligence in manufacturing, automated quality assurance is a major topic of discussion.
Traditionally, manufacturers have used manual quality assurance techniques to “catch” issues before they leave the factory.
But as manufacturing processes become increasingly complex, these manual techniques can be laborious and time-consuming, and oftentimes difficult to keep up with.
That’s why automated quality assurance is being touted as the future of manufacturing.
Through the use of AI-driven technologies, automated quality assurance provides a more reliable way to detect minor issues before products leave the factory.
These automated systems use techniques such as real-time analytics and predictive analytics to monitor products continuously throughout the production process and identify any potential problems early on.
Automated systems can also be used to detect potential defects in the raw materials used in the manufacturing process.
In addition to the speed and efficiency of automated quality assurance, one of its greatest benefits is that it detects issues that would be otherwise invisible to manual inspection.
By streamlining processes and proactively optimizing production, AI-driven systems provide a more cost-effective and reliable way to guarantee that customers get the best products.
2. Automated Process Monitoring
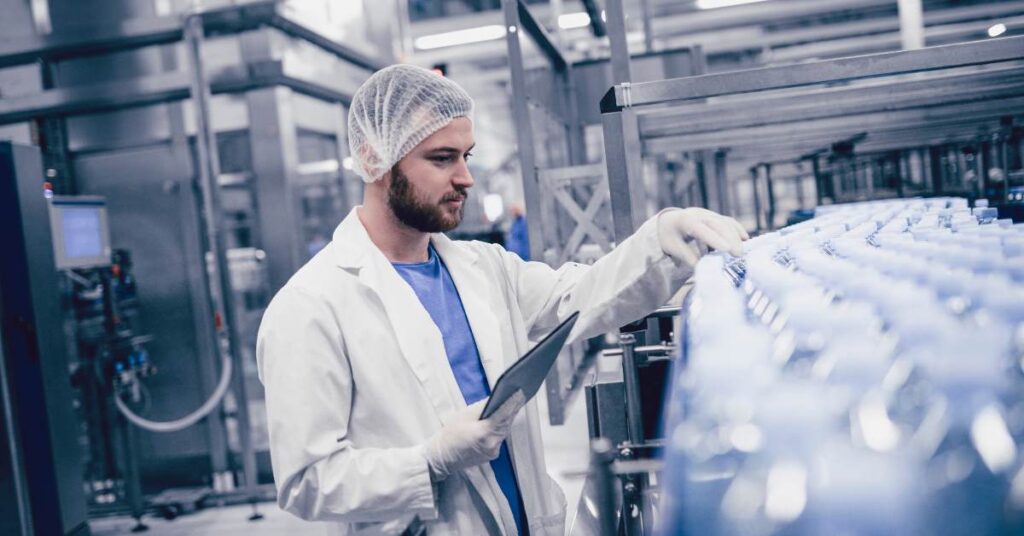
Process monitoring involves monitoring the manufacturing to ensure integrity, accuracy, and efficiency of the operations.
For many years, the manufacturing process has primarily relied on manual monitoring to observe and document quality and performance. But this is no longer tenable with the explosion of big data. Deloitte estimates that manufacturers alone generate about 1,800 petabytes of data every year.
Automated process monitoring is replacing the labor-intensive manual procedures with machines that are programmed to accurately monitor production data, automatically recording the data into the system.
This technology helps catch any discrepancies in the process quickly and affords manufacturers the tools to track and analyze their operations in real-time.
Epirus Systems, wanted to improve manufacturing throughput and material visibility at their factory in Hawthorne, CA.
By leveraging the ION’s analytics engine by First Resonance, they were able to improve their factory workflows through automated real-time data collection and visualization, thereby saving 12 hours per month per engineer.
Apart from the increased accuracy and efficiency of their manufacturing process, the implementation of automated process monitoring also brought other benefits, such as improved process speed and reduced costs.
Overall, automated process monitoring is set to revolutionize the manufacturing industry over the coming years.
With its ability to accurately document and record data, as well as optimize factory workflows with data visualization, manufacturers can look forward to a more efficient and cost-effective approach to their business operations.
3. Predictive Maintenance
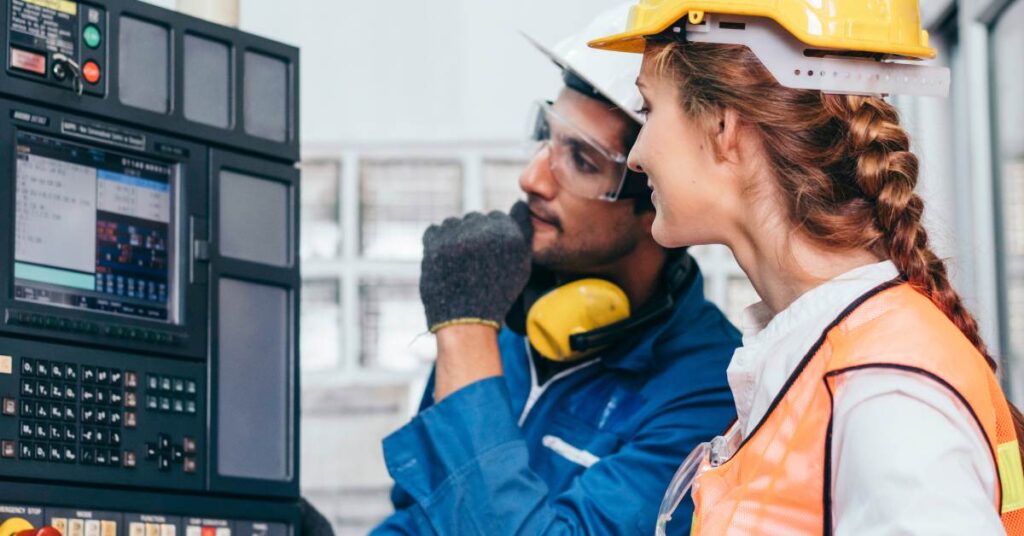
The industrial landscape is ripe for change.
With advancements in cutting-edge technologies, many manufacturers are turning to predictive maintenance methods to streamline operations. Predictive maintenance is an attractive alternative to traditional maintenance procedures.
Whereas traditional methods require machines to be physically inspected on a regular basis to identify problems, predictive maintenance relies on data and analytics to provide manufacturers with information on when maintenance is needed.
This is made possible by the use of monitored sensors, machine learning programs, and real-time data collection tools.
By capturing data related to the performance of machines, predictive maintenance systems can detect anomalies and forecast when preventive maintenance needs to be carried out.
It helps to reduce downtime, which in turn lowers overall costs. Automation tools also eliminate human error, making maintenance procedures more reliable.
While the advantages of predictive maintenance are clear from a business standpoint, there may be wider implications. As predictive maintenance methods become more widespread, it could bring about changes not only in manufacturing but also in terms of employment opportunities.
In an era where automation is a regular occurrence, predictive maintenance could eventually lead to job displacement. That said, this also could open up opportunities in different sectors such as data analysis and software engineering.
4. Automated Scheduling
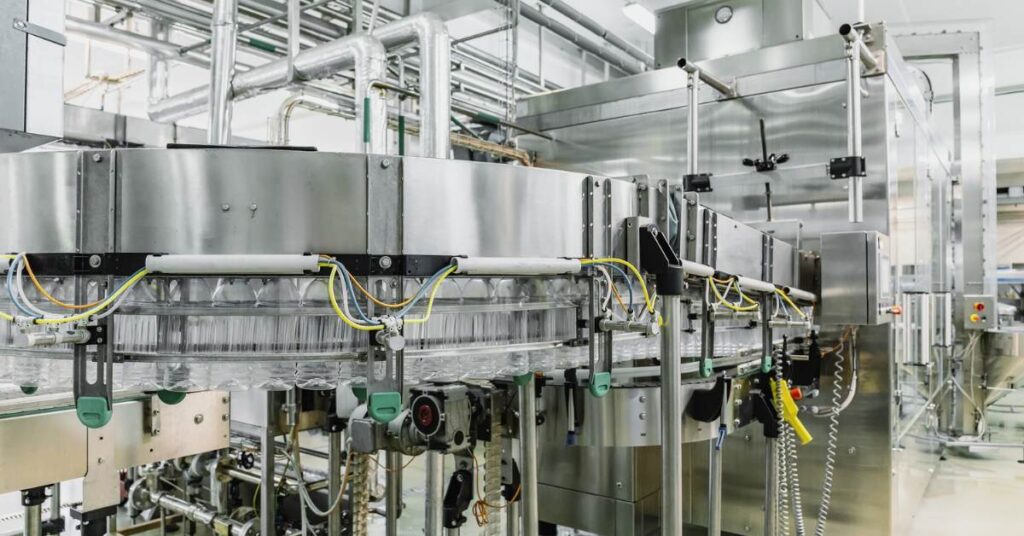
Manual scheduling used to be a laborious task for factories.
However, automated scheduling systems allow manufacturing managers to save time and energy while still ensuring their production lines are running efficiently.
Manual scheduling involves creating a task list, assigning resources, and ensuring tasks are completed on time and with the right resources – all while ensuring a cohesive workflow.
Automating this process with a computer program streamlines the task and eliminates any possibility of human error.
Automatic scheduling systems use algorithms to predict completion times, assign tasks to machines and personnel, and rearrange tasks if there are any snags in the production process.
This ensures that things run on schedule more quickly and efficiently. The result is a production line that is more dynamic and agile, and can better meet any fluctuations in demand.
Say YES to increased productivity, improved safety, and reduced costs.
This is the foundation of the future of manufacturing — efficient production that not only saves time and energy, but also provides a secure, reliable machine that is capable of augmenting human labor.
Automated scheduling systems transform manual processes into a streamlined operation, and this is key to survival in the competitive global market.
5. Improved Supply Chain Optimization

It’s no secret that many factories suffer from supply chain problems due to non-optimized routes or delays or supply quality issues.
At its core, supply chain automation works by data collection and analysis.
Data is collected from machines and by analyzing this data, AI can provide insights into the overall efficiency and performance of the supply chain.
The most obvious benefit to AI-driven supply chain optimization is a reduction in costs.
It can make processes faster and more efficient, thus eliminating the need for human labor. Additionally, AI-driven supply chains can reduce the risk of errors that can otherwise lead to costly delays.
For an example of this in action, one need look no further than Hitachi.
The company has implemented an AI-driven supply chain solution in their factories, where they use sensors and data analysis to identify production delays and areas for improvement. The result is a noticeably more efficient process, which translates into reduced costs and higher profits.
Not only does automation reduce costs and improve efficiency, but it also helps companies stay ahead in an ever-changing market. Those companies that do not invest in AI and automation will be knocked out, steam-rolled, and kicked into oblivion.
Conclusion
We’ve seen the tremendous potential of Artificial Intelligence and automation when it comes to manufacturing.
From improved efficiency and cost savings to greater accuracy and precision in manufacturing processes, AI has already had a powerful impact.
However, the journey is far from over.
Deloitte conducted a survey and established that 93% of manufacturers look to AI as the pivotal technology for driving growth and innovation in factories.
AI-powered automation will continue to revolutionize the manufacturing industry, but there are still three major problems that need to be solved.
From recognizing and preventing worker displacement, to ensuring safe and secure digital systems, we need to devise ways to make sure that AI and automation are used ethically and responsibly.
As we move towards a future where AI and automation play an increasingly larger role in the manufacturing industry, we need to ensure that these solutions are created and implemented with the wellbeing of workers and our planet in mind.
Let’s take the initiative and continue to work towards achieving a sustainable and ethical future in manufacturing.